Injection molding and compression molding are both plastic manufacturing processes. They differ in several key aspects. They are as follows.
Definition Comparison:
What is Compression Molding ?
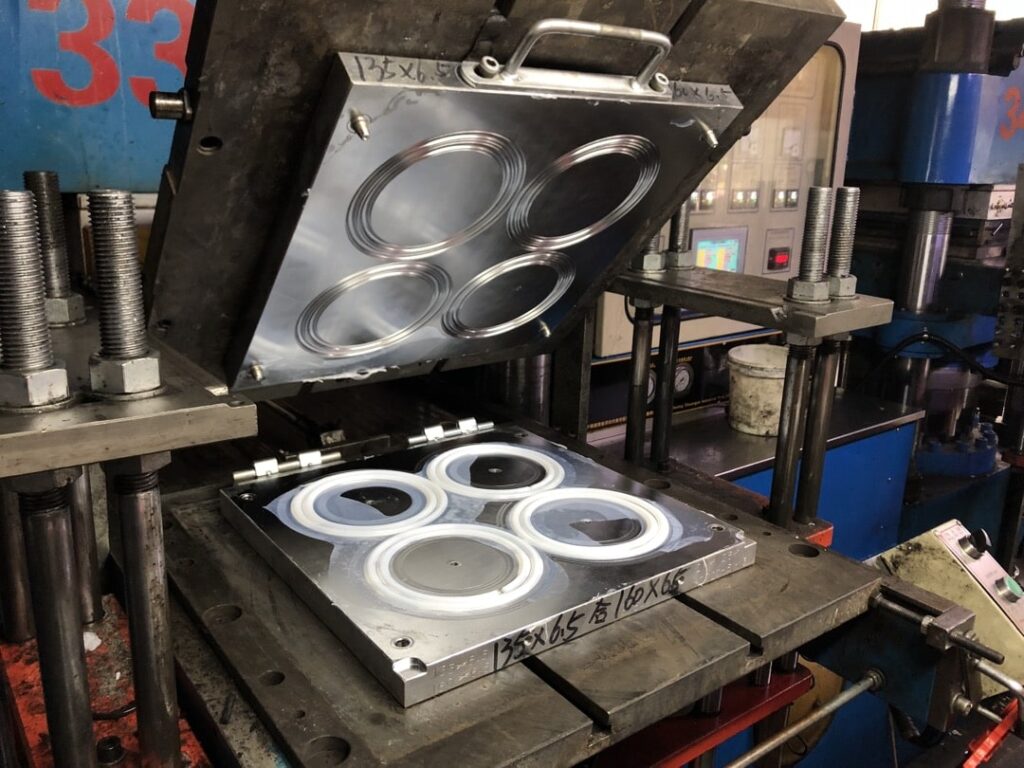
Compression Molding is a process of placing a pre-measured plastic sheet or preform into a heated mold. And then compressed under high pressure.
What is Injection Molding?
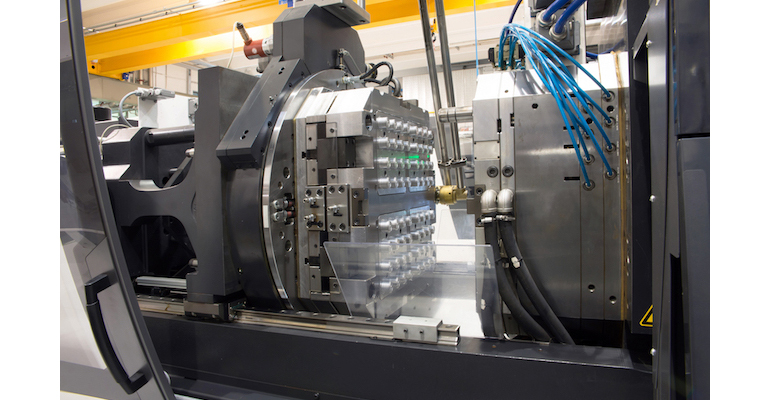
Injection Molding is the process of melting plastic pellets and injecting the molten material into a mold cavity.
Key Differences between Compression Molding and Injection Molding:
- Compression molding starts with the plastic material in the mold, while injection molding involves melting plastic pellets separately.
- Compression molding applies pressure to shape the material into the desired form while injection molding uses pressure to inject the molten plastic into the mold.
- Compression molding is often used for thermosetting materials. Whereas injection molding is mostly used for thermoplastic materials
- Injection molding is suitable for more complex and precise part geometries, while compression molding is better suited for simpler shapes.
Differences in Applications:
Compression Molding:
- Compression Molding finds its applications where the parts needed to be durable and strong with simpler geometry.
- It is used in manufacturing, Brake pads, body panels, sporting goods, electrical switches, toys, etc.
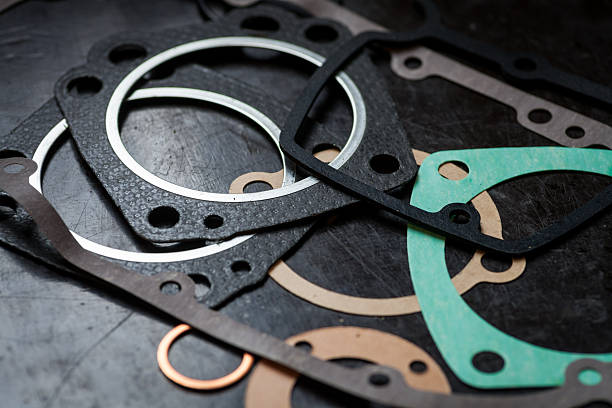
Injection Molding:
- Injection molding finds its applications where the parts are intricate and need to be precise.
- It is used in manufacturing, door panels, furniture like chairs and small tables, and even medical instruments like syringes and orthopedic implants
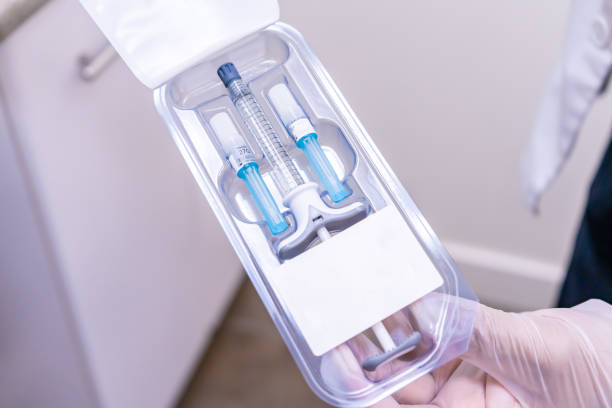
Comparison Table:
Compression Molding and Injection Molding
Compression Molding | Injection Molding | |
Material Compatibility | Ideal for thermosetting material and composites. | Ideal for a wide range of thermoplastic materials. |
Tooling Cost | Generally lower initial tooling costs, due to simpler molds. | Involves higher tooling costs, especially for complex parts |
Cycle Time | It offers longer cycle times due to heating and cooling stages. | Higher production rates and provide shorter cycle times |
Waste Minimization | It generally generates less material waste, but in some cases, may generate more material waste, as excess material often requires trimming. | Generate less waste due to precise control over material placement. |
Complex Part Geometries | It is best suited for simpler part geometries. | It is capable of producing complex and highly detailed parts. |
Production Volume | Typically used for low to medium production volume. | Ideal for high-volume production due to faster cycle times. |
Precision and Consistency | Tends to have lower precision and consistency in part dimensions. | Offers high precision and consistent part quality. |
Initial Setup Time | This process may require longer setup times due to manual material placement | This process is generally quicker to set up, especially for automated systems. |
Part design Flexibility | Its design flexibility is limited to intricate parts | Offers great design flexibility for complex shapes and features. |
These are the major differences between compression molding and injection molding.
Conclusion:
In summary, Injection molding is suitable for complex parts and high-volume production but comes with higher tooling costs. Compression molding is more cost-effective for thermosetting materials and simpler parts. But it has a longer cycle time.
The choice between the two methods should be based on the specific requirements of the project.
And,
Are you facing challenges in these manufacturing processes?
At TOPGRID, we provide you with 50+ manufacturing processes. And end-to-end manufacturing services starting from initial design to final product completion at the best prices, lead times, and quality!
Get your quote today!!
Topgrid – Injection Molding Service
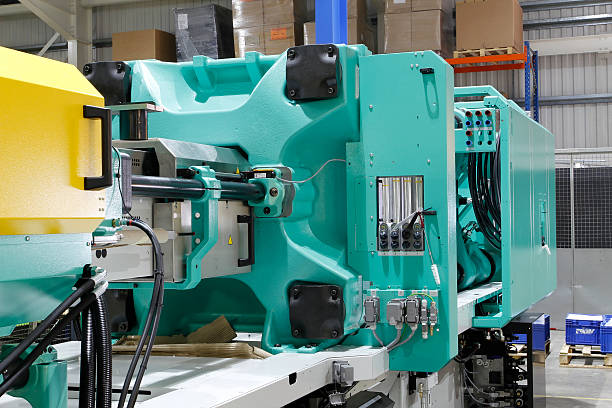
- At Topgrid, we pride ourselves on being a best provider of Plastic Injection Molding Services.
- With a strong commitment to precision, innovation, and customer satisfaction, we are your trusted partner for all your plastic injection molding needs.
- Our dedication to staying at the forefront of technology and industry trends ensures that we can meet the unique requirements of each project, no matter how complex.
Topgrid – Compression Molding Service
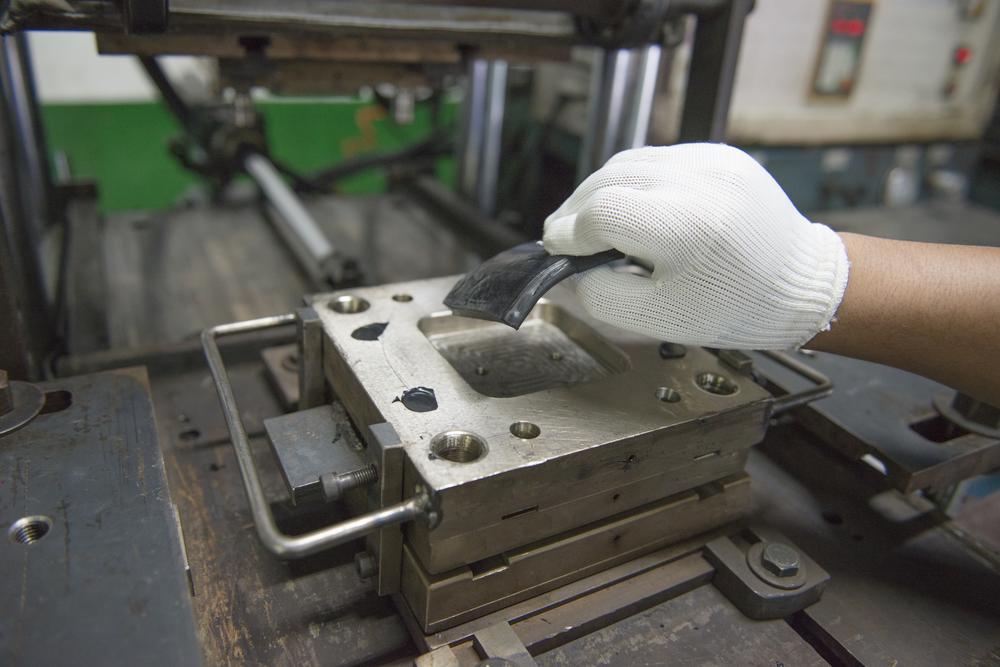
- At Topgrid, we take immense pride in being a best provider of Compression Molding Services.
- Topgrid’s experienced engineers can help you design and manufacture custom molds to meet your specific needs.
- Topgrid’s experienced engineers can help you design and manufacture custom molds to meet your specific needs that optimizes quality and efficiency.
Related Blogs
Centrifugal Casting – Definition, Process, Types and Applications
Centrifugal casting is a versatile and efficient metal casting process used to create high-quality, thin-walled cylindrical parts. It uses centrifugal force…
Semi Centrifugal Casting – Definition, Process, Advantages and Applications
Semi centrifugal casting is a specialized metal casting process that combines gravity pouring with centrifugal force to produce high-quality castings. …
Low Pressure Die Casting – An Overview
Low pressure die casting (LPDC) is one of the metal casting processes. It uses low pressures to force molten metal…
High Pressure Die Casting – Definition, Process, Application, Advantage, etc
High-pressure die casting (HPDC) is a manufacturing process that involves injecting molten metal into a steel mold die under high…
Gravity Die Casting – Definition, Gravity Die Casting Process, Application, etc.
Gravity die casting plays a vital role in various industries, shaping the world around us. From the cars we drive…