Centrifugal casting is a versatile and efficient metal casting process used to create high-quality, thin-walled cylindrical parts. It uses centrifugal force generated by the rotation of a mold to distribute molten metal evenly throughout the cavity.
Now let’s learn more about it in this article.
This article will give you insights into,
- What is Centrifugal Casting?
- Centrifugal Casting Process:
- Types of Centrifugal Casting:
- True Centrifugal Casting:
- Semi Centrifugal Casting:
- Centrifuge Casting:
- Types of Centrifugal Casting Machines:
- Horizontal Centrifugal Casting Machines:
- Vertical Centrifugal Casting Machines:
- Advantages of Centrifugal Casting:
- Disadvantages of Centrifugal Casting:
- Applications of Centrifugal Castings:
- Conclusion:
- How TOPGRID can help you ?
What is Centrifugal Casting ?
Centrifugal casting is a metal casting process where molten metal is poured into a rotating mold. This creates a centrifugal force that distributes the metal evenly throughout the cavity. And results in producing a cylindrical or symmetrical part.
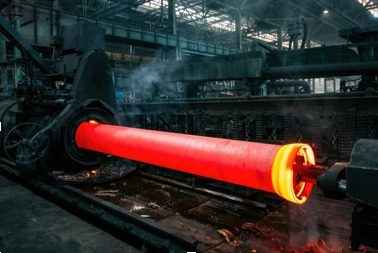
Centrifugal casting is commonly used for manufacturing pipes, tubes, and cylindrical components.
Now, before choosing a casting service, you must know about the process yourself. The work principle of the centrifugal casting method is as follows.
Centrifugal Casting Process:
The step-by-step process of centrifugal casting is as follows:
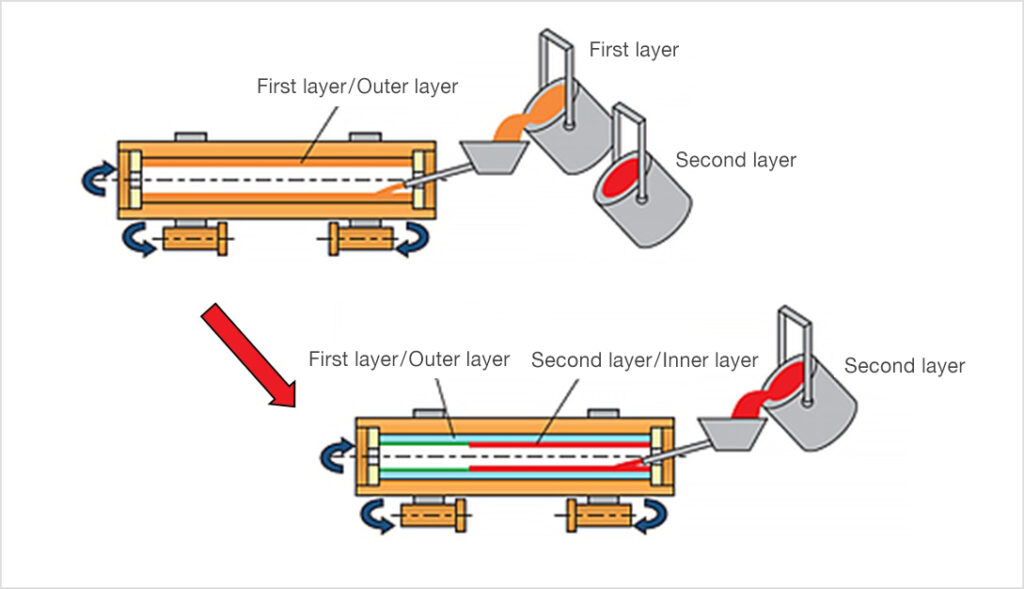
Step:1
Mold Preparation:
The mold typically made of metal or ceramic, is coated with a refractory material. This helps the mold to withstand the high temperatures of the molten metal.
Step:2
Rotation:
The mold is mounted on a rotating spindle and set to spin at high speeds. The rate of rotation is typically between 300 and 3000 rpm.
Step:3
Preparing the Metal:
Just like any casting method, the metal is heated and melted to its liquid state in a separate furnace, maintaining the desired pouring temperature.
Step:4
Pouring:
Molten metal is poured into the rotating mold. Centrifugal force pushes the molten metal outward against the mold walls. This creates a uniform and dense casting.
Step:5
Solidification:
The mold continues to rotate as the molten metal cools and solidifies. The centrifugal force helps to remove air bubbles and impurities from the metal. And, the rotation ensures a consistent wall thickness, resulting in a sound casting with good mechanical properties.
Step:6
Cooling and Removal:
After the metal gets solidified, the mold is stopped and the casting is removed. Additional finishing processes, such as machining or surface treatments are performed if necessary.
Thus these are the steps involved in centrifugal casting. The initial steps are very similar to other regular casting processes like Gravity Die Casting.
And, If you’re looking for more die casting, you may check out our High-Pressure Die Casting and Low-Pressure Die Casting.
Types of Centrifugal Casting:
There are three main types of centrifugal casting methods. The best type of this method depends on your specific production requirements.
This concise guide will give you an overview of each type of the centrifugal casting process.
True Centrifugal Casting:
- In true centrifugal casting, the mold is positioned horizontally. Here the axis of rotation is parallel to the axis of the casting.
- The molten metal is poured into the rotating mold through a central sprue. As the mold spins, centrifugal force pushes the molten metal outward. This forms a hollow cylinder around the central sprue.
- It has the advantages of producing parts with uniform wall thickness and improved metallurgical properties. It is well-suited for mass production of cylindrical components, making it cost-effective for certain applications.
- True centrifugal casting also comes with certain limitations. Like, it is limited to cylindrical or symmetrical shapes. And may not be suitable for producing extremely thin-walled parts.
- This process is ideal for producing long, hollow cylindrical parts, such as pipes and tubes.
Semi Centrifugal Casting:
- In semi centrifugal casting, the mold is positioned vertically. And, here the axis of rotation is perpendicular to the axis of the casting.
- In this process, the molten metal is poured into the mold from the top. Centrifugal force distributes the molten metal around the mold walls. Here gravity also plays a role in filling the mold cavity.
- The semi centrifugal casting method has several advantages. It is more versatile than true centrifugal casting, allowing for the production of parts with non-cylindrical shapes. And, can accommodate a range of part sizes, from small components to larger structures.
- It has a few limitations too. This process may result in less uniform wall thickness compared to true centrifugal casting. And, the quality of castings may vary depending on factors like rotation speed, mold design, and metal temperature.
- The semi centrifugal casting process is suitable for casting shorter, thicker-walled parts, such as wheels and gears.
Centrifuge Casting:
- The centrifuge casting process involves using a centrifuge machine to distribute molten metal within a mold using centrifugal force.
- Similar to other casting methods, the metal is melted and poured into a mold. The mold is placed in a centrifuge machine that rapidly spins, creating centrifugal force. It evenly distributes molten metal in the mold, creating a smooth and uniform surface finish. Once cooled, the centrifuge stops and the casting is removed.
- This method is effective for small and complicated parts without needing any post-processing.
- Centrifuge casting is commonly used for producing small and detailed components. It finds its applications in industries like jewelry making, dental casting, and certain specialized manufacturing processes.
Types of Centrifugal Casting Machines:
When choosing a manufacturing process you may get confused about the type of machines that suits your project.
Here, when it comes to choosing a centrifugal casting method, you have primarily two options, horizontal centrifugal casting machine and vertical centrifugal casting machine. The key difference between them is their axis of rotation.
An overview of both the types are as follows.
1. Horizontal Centrifugal Casting Machines:
- In horizontal centrifugal casting machines, the mold rotates horizontally around a central axis.
- This machine is ideal for casting long, thin-walled cylindrical parts. Such as pipes, shafts, and tubes.
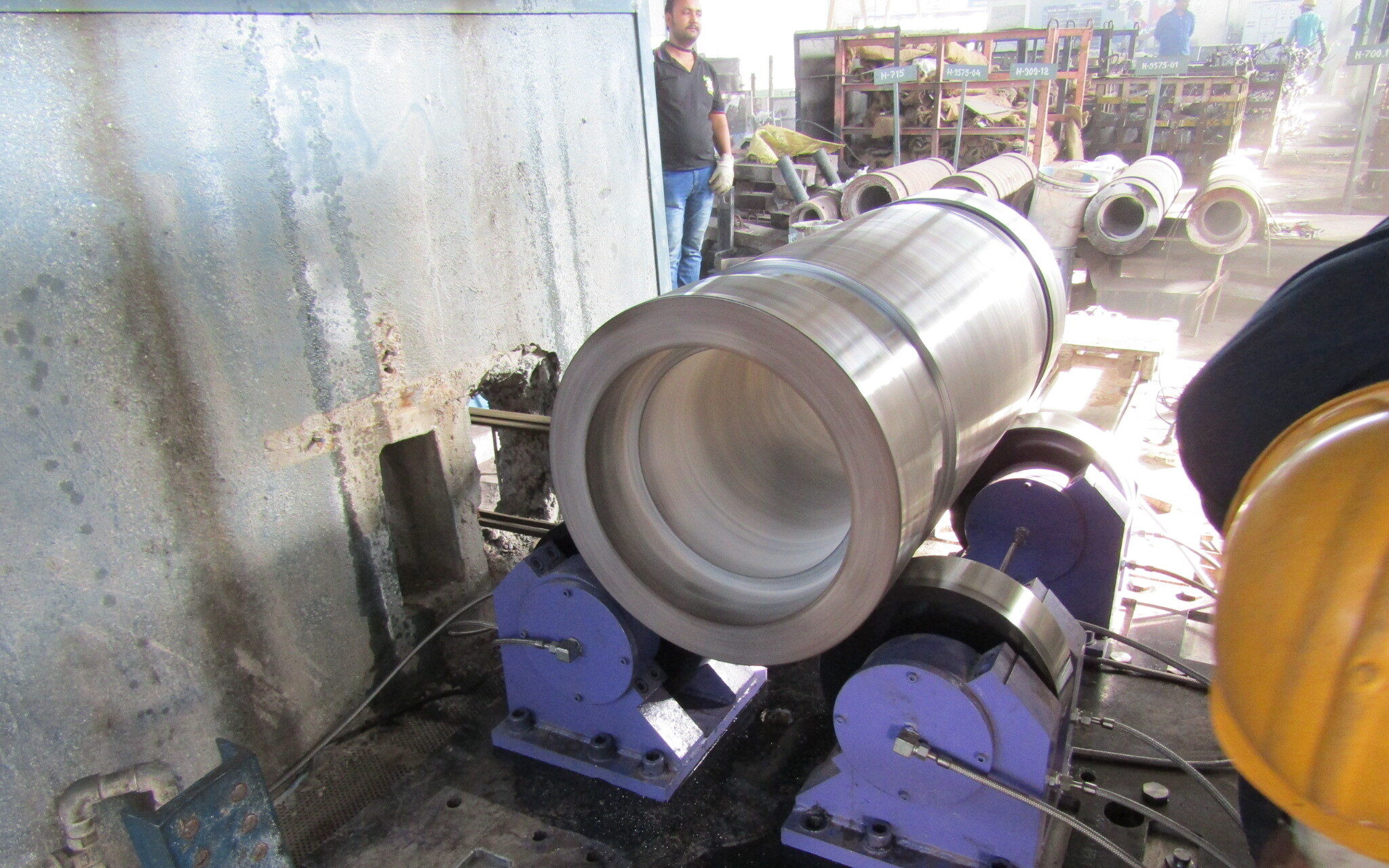
This machine has a few advantages like,
- It can efficiently produce long, straight parts.
- It is easier to pour molten metal into the mold compared to vertically positioned molds.
It comes with a few limitations too. They are,
- This machine is not suitable for casting parts with complex geometries.
- It requires additional support structures for longer molds.
2. Vertical Centrifugal Casting Machines:
- In vertical centrifugal casting machines, the mold rotates vertically around a central axis.
- This machine is suitable for casting shorter, thicker-walled parts. Like, rings, wheels, and gears.
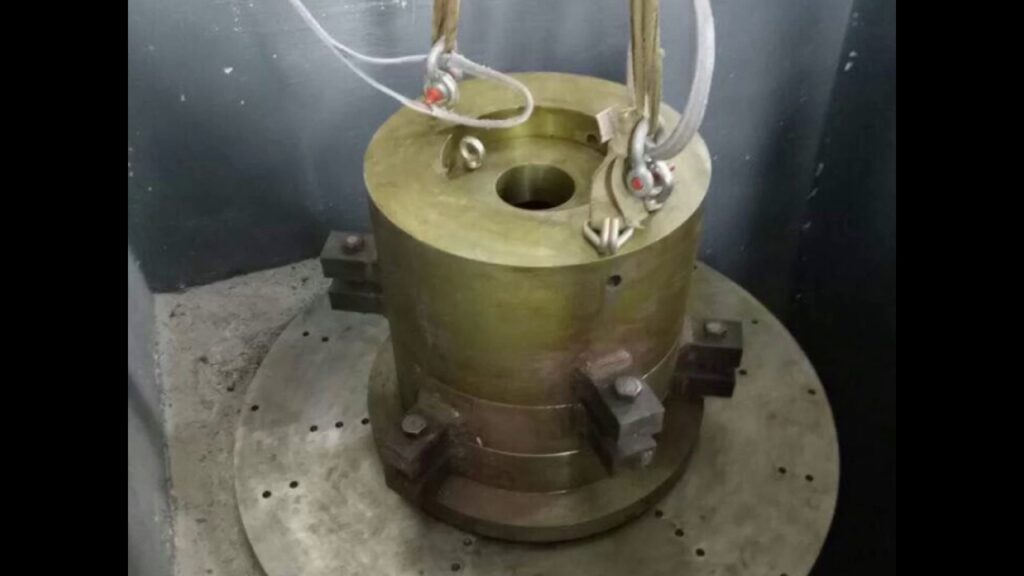
A few advantages of using vertical centrifugal casting machines are,
- This machine can accommodate parts with more complex geometries.
- It is less prone to material segregation compared to horizontal machines.
- It is easy to access and remove the finished casting from this machine.
And, a few disadvantages of using this machine is,
- Obviously less efficient for casting long, thin-walled parts compared to horizontal centrifugal casting machines.
- It requires careful control of pouring to prevent spills.
- It can be more challenging to remove air bubbles from the mold cavity. \
In summary,
Both the horizontal and vertical centrifugal casting machines come with their unique advantages and disadvantages. And, you need to choose the one that suits your project based on the factors like specific requirements of your parts and your production volume.
If you’re considering using any of these machines for your next project, be sure to contact a manufacturing consultant to discuss your specific needs.
Next,
When choosing or learning about manufacturing processes you need to consider both the benefits and limitations of it. That helps you in better decision-making, minimizing costs, and ensuring the quality of your products.
Let’s look at the advantages and disadvantages of the centrifugal casting process.
Advantages of Centrifugal Casting:
A few advantages you can consider when choosing centrifugal casting are,
- Centrifugal casting produces castings with excellent surface finish and dimensional accuracy.
- This process uses molten metal effectively. This minimizes material waste and reduces costs.
- The high pressure applied by centrifugal force promotes the formation of a fine and equiaxed grain structure. This leads to strong and sound castings.
- Centrifugal casting is a versatile process. It can be used to cast a wide range of metals, including iron, steel, aluminum, bronze, and copper.
- The process is easily automated. Hence making it more suitable for high-volume production.
Disadvantages of Centrifugal Casting:
Like both sides of the coin, there are disadvantages too, which you must consider before choosing it.
A few disadvantages of centrifugal casting are,
- This process is limited to cylindrical shapes or parts with rotational symmetry.
- In certain alloys with different component densities, centrifugal force can lead to segregation. This results in heavier elements concentrating towards the outer edges of the castings. This affects the mechanical properties of the final product.
- May not be suitable for very small or complex parts.
- While the outer surface of centrifugally cast parts typically exhibits a smooth finish, the inner surface can be rough due to contact with the mold walls.
Applications of Centrifugal Castings:
Centrifugal casting offers several unique advantages. Hence centrifugal casting is done for producing various parts for various applications.
Here are some of the most common applications of this process:
Pipes and Tubes:
Centrifugal casting is done for producing seamless pipes and tubes, including:
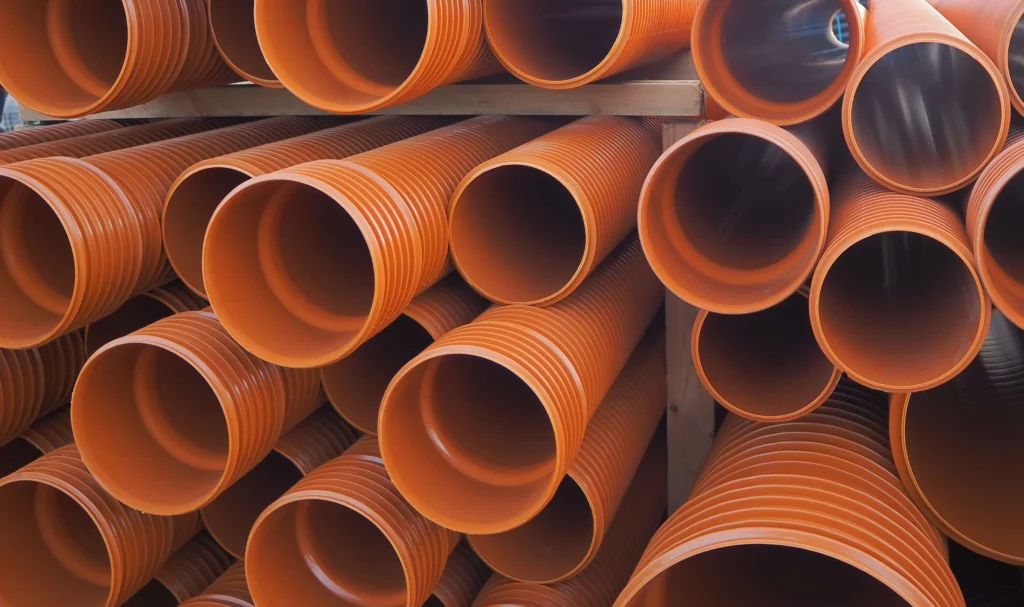
- Lamp posts
- Sewage pipes
- Water supply lines
- Oil and gas pipelines
- Boiler tubes Hydraulic cylinders
Rings and Wheels:
The centrifugal casting process is ideal for creating high-strength and dimensionally accurate rings and wheels, such as:
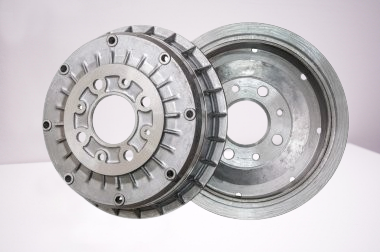
- Gears
- Bearings
- Flywheels
- Brake drums
- Railroad wheels
Cylindrical Parts:
This process is suitable for producing various cylindrical parts, including:
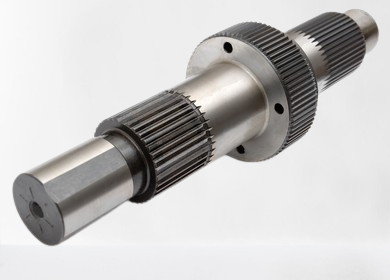
- Liners
- Shafts
- Rollers
- Sleeves
- Bushings
Other Applications:
The centrifugal casting process can also be used to create a variety of other parts, such as:
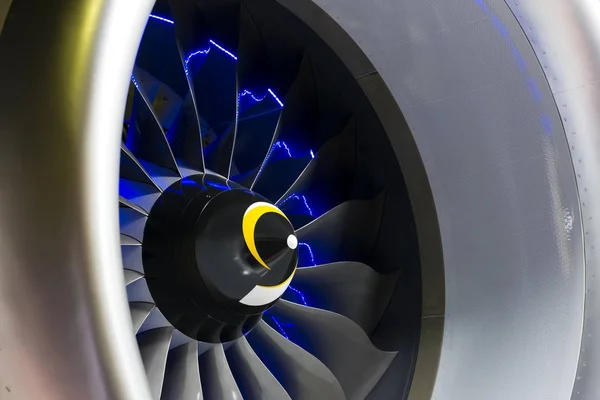
- Valve bodies
- Turbine blades
- Missile casings
- Pump housings
- Medical implants
- Aerospace components
Conclusion:
In conclusion, centrifugal casting is a valuable and versatile process for producing high-quality parts across various industries. If you’re looking to produce seamless pipes, robust gears, intricate turbine blades, or any other cylindrical components, centrifugal casting presents a powerful tool for your manufacturing needs.
Understanding the specific requirements of your project and consulting the manufacturing specialist or experts are crucial for determining whether this process is a suitable method.
Topgrid – Centrifugal Casting Services
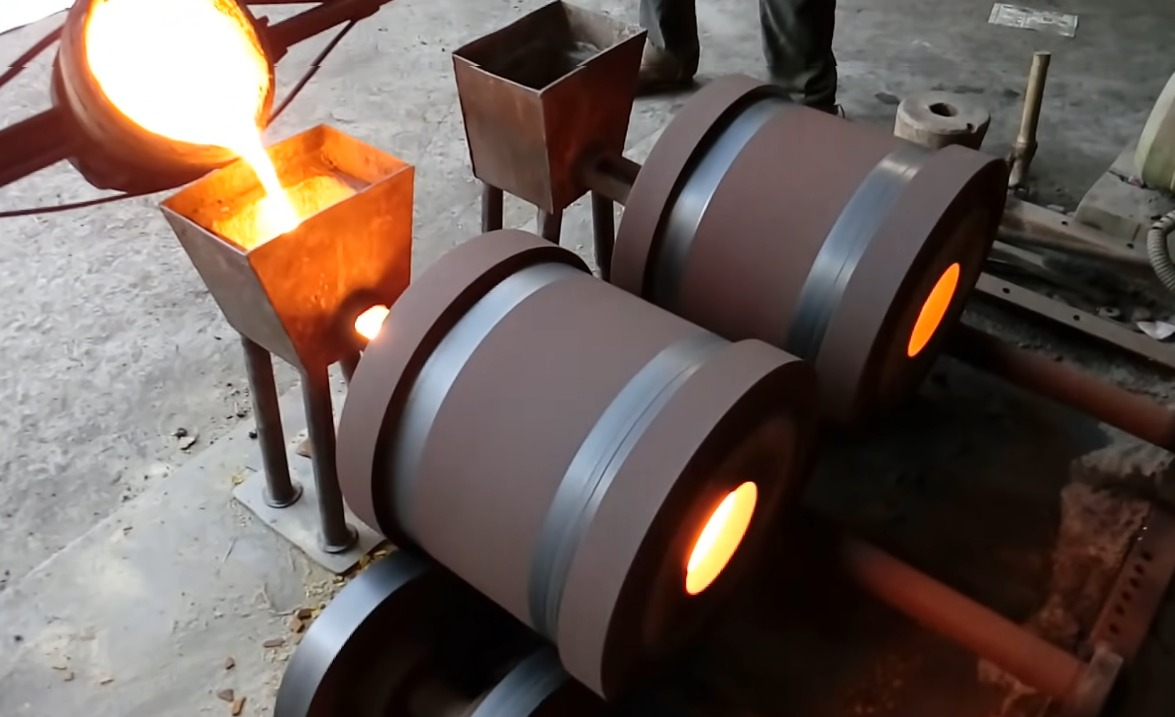
- At Topgrid, we pride ourselves on being a best provider of Centrifugal Casting Services.
- Topgrid’s Centrifugal casting services are ideal for a wide range of industries, including automotive, aerospace, electronics, medical, and consumer goods.
- If you are looking for a high-quality, reliable Centrifugal provider, contact Topgrid today.